42CrMo seamless steel pipe belongs to ultra-high strength steel, with high strength and toughness, good hardenability, no obvious tempering brittleness, high fatigue limit and multi impact resistance after quenching and tempering, and good low-temperature impact toughness.
The steel is suitable for manufacturing large and medium-sized plastic molds requiring certain strength and toughness. Its corresponding ISO brand: 42CrMo4 corresponds to Japanese brand: scm440 corresponds to German brand: 42CrMo4 approximately corresponds to American brand: 4140 characteristics and scope of application: high strength, high hardenability, good toughness, small deformation during quenching, and high creep strength and endurance strength at high temperature. It is used to manufacture forgings with higher strength and larger quenched and tempered cross-section than 35CrMo steel, such as large gears for locomotive traction, supercharger transmission gears, rear shafts, connecting rods and spring clips with great load, drill pipe joints and fishing tools for oil deep wells below 2000m, and molds for bending machines.
Chemical composition of 42CrMo seamless steel pipe: c: 0.38% - 0.45%, si: 0.17% - 0.37%, mn: 0.50% - 0.80%, cr: 0.90% - 1.20%, mo: 0.15% - 0.25%, Ni ≤ 0.030%, P ≤ 0.030%, s ≤ 0.030%
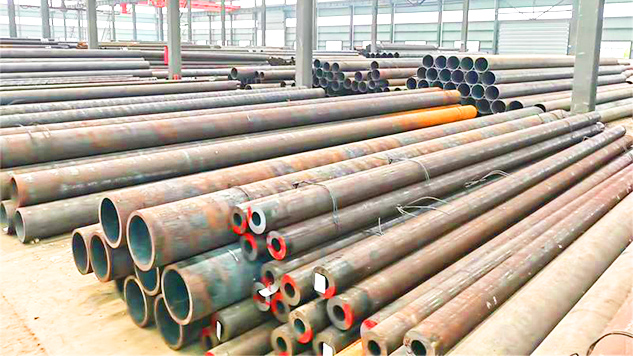
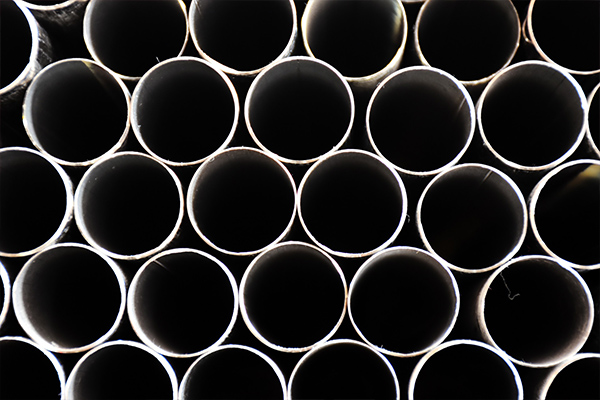
The role of various chemical elements in steel pipes:
Carbon (c): in steel, the higher the carbon content, the higher the strength and hardness of steel, but the plasticity and toughness will also be reduced; On the contrary, the lower the carbon content, the higher the plasticity and toughness of steel, and its strength and hardness will also be reduced.
Silicon (SI): added to ordinary carbon steel as deoxidizer. Proper amount of silicon can improve the strength of steel without significant adverse effects on plasticity, impact toughness, cold bending performance and weldability. Generally, the silicon content of killed steel is 0.10% - 0.30%, and too high content (up to 1%) will reduce the plasticity, impact toughness, rust resistance and weldability of steel.
Manganese (MN): it is a weak deoxidizer. An appropriate amount of manganese can effectively improve the strength of steel, eliminate the influence of sulfur and oxygen on the hot brittleness of steel, improve the hot workability of steel, and improve the cold brittleness tendency of steel, without significantly reducing the plasticity and impact toughness of steel. The content of manganese in ordinary carbon steel is about 0.3% - 0.8%. Too high content (up to 1.0% - 1.5%) makes the steel brittle and hard, and reduces the rust resistance and weldability of the steel.
Chromium (CR): it can improve the strength and hardness of carbon steel in rolling state. Reduce elongation and reduction of area. When the chromium content exceeds 15%, the strength and hardness will decrease, and the elongation and reduction of area will increase correspondingly. Parts containing chromium steel are easy to obtain high surface processing quality after grinding.
The main function of chromium in quenched and tempered structural steel is to improve hardenability. After quenching and tempering, the steel has better comprehensive mechanical properties, and chromium containing carbides can be formed in carburized steel, so as to improve the wear resistance of the material surface. Chromium is one of the important elements in stainless steel, which mainly improves the rust prevention, hardness and wear resistance of steel.
Molybdenum (MO): molybdenum can refine the grain of steel, improve hardenability and thermal strength, and maintain sufficient strength and creep resistance at high temperature (long-term stress and deformation at high temperature, called creep). Adding molybdenum to structural steel can improve mechanical properties. It can also inhibit the brittleness of alloy steel caused by fire.
Sulfur: harmful element. It will cause hot embrittlement of steel and reduce the plasticity, impact toughness, fatigue strength and rust resistance of steel. The sulfur content of steel for general construction shall not exceed 0.055%, and it shall not exceed 0.050% in welded structures. Phosphorus: harmful element. Although it can improve strength and rust resistance, it can seriously reduce plasticity, impact toughness, cold bending performance and weldability, especially cold embrittlement at low temperature. The content should be strictly controlled, generally not more than 0.050%, and not more than 0.045% in welded structures. Oxygen: harmful element. Cause hot brittleness. Generally, the content is required to be less than 0.05%. Nitrogen: it can strengthen the steel, but significantly reduce the plasticity, toughness, weldability and cold bending properties of the steel, and increase the aging tendency and cold brittleness. Generally, the content is required to be less than 0.008%.
Post time: Aug-11-2022